Designing High-Efficiency Cleanrooms for Pharmaceutical Production
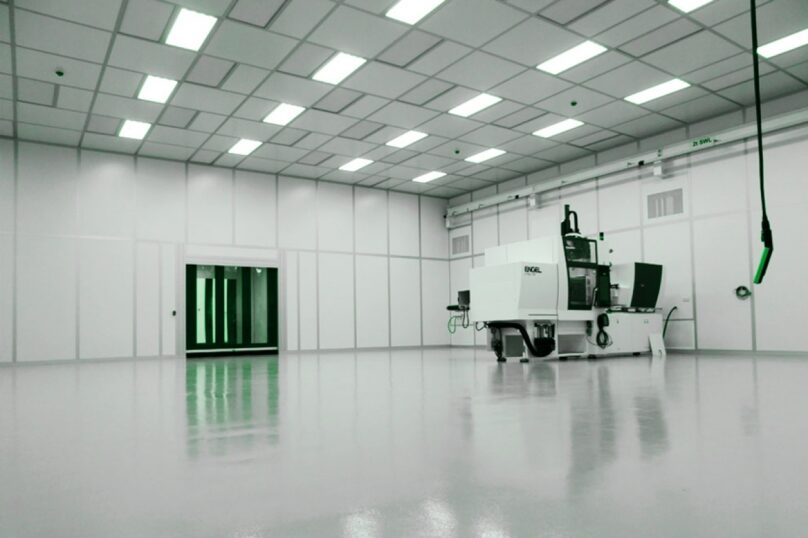
In pharmaceutical manufacturing, product purity isn’t just a quality measure—it’s a regulatory requirement. One of the most critical elements in achieving contamination-free environments is the cleanroom. As pharmaceutical products become more complex and regulatory scrutiny intensifies, designing high-efficiency cleanrooms is no longer optional—it’s essential.
At JD Engineers & Consultants, we bring over two decades of expertise in pharmaceutical facility design. Our cleanroom solutions are engineered to meet international standards, optimize operational efficiency, and ensure total compliance with Good Manufacturing Practices (GMP).
What Is a Cleanroom—and Why It Matters?
A cleanroom is a controlled environment designed to limit contamination from airborne particles, microbes, and other pollutants. It plays a key role in manufacturing sterile and sensitive pharmaceutical products such as:
- Tablets and capsules
- Injectable drugs
- Biopharmaceuticals
- APIs (Active Pharmaceutical Ingredients)
Without proper cleanroom design, manufacturers face high risks of product recalls, regulatory action, and, most importantly, harm to patients.
Key Elements of High-Efficiency Cleanroom Design
1. Air Filtration & HVAC Systems
At the core of cleanroom performance is its air handling system. We use HEPA/ULPA filters that trap 99.97% of particles ≥0.3 microns and design HVAC systems that maintain the right air pressure differentials (positive or negative) to control contamination.
✅ What We Provide:
- Pressure zoning
- Temperature and humidity control
- Energy-efficient air circulation
- Real-time monitoring systems
2. Modular Cleanroom Construction
Modular cleanrooms offer flexibility, scalability, and faster installation. Our prefabricated panels are made with antimicrobial materials and ensure seamless, smooth surfaces that are easy to clean and maintain.
✅ Benefits:
- Reduced downtime
- Customizable layout
- Faster project execution
3. GMP & Regulatory Compliance
Our designs comply with WHO-GMP, USFDA, MHRA, and EU cGMP standards. We provide full documentation, validation support, and audit-readiness services to make sure your facility meets both local and international regulations.
4. Material & Personnel Flow
One of the most overlooked aspects of cleanroom design is movement control. Our cleanrooms are engineered to separate clean and dirty workflows to prevent cross-contamination.
✅ Features:
- Pass boxes & airlocks
- Gowning/de-gowning areas
- Material transfer protocols
- Unidirectional flow paths
5. Integrated Automation
Modern cleanrooms require more than just clean air—they need smart controls. We incorporate Building Management Systems (BMS) and SCADA solutions to give operators complete control over HVAC, lighting, temperature, pressure, and access control from a central dashboard.
Why JD Engineers & Consultants?
With successful projects in 13+ countries, we are among the few Indian engineering consultants with true global reach. Our cleanroom solutions are trusted by pharmaceutical companies across India, the Middle East, Africa, Southeast Asia, and the USA.
What sets us apart:
- Over 23 years of consulting experience
- Deep knowledge of pharmaceutical processes
- In-house multidisciplinary team
- Turnkey project execution—from design to validation
Conclusion
In an industry where quality and compliance are non-negotiable, a high-efficiency cleanroom is the backbone of pharmaceutical production. At JD Engineers & Consultants, we don’t just design cleanrooms—we build precision environments that power global health.